Schoeller Allibert optimises processes for apparel company Peek & Cloppenburg Stack&nest containers replace cardboard
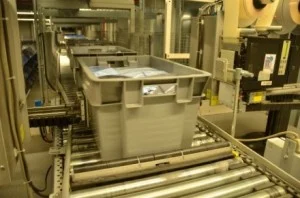
Peek & Cloppenburg has been operating a large logistics centre in Reinbek, Hamburg, since 2009. The 35,000 square metre facility boasts the most advanced rack and conveying systems, employing ultra-modern, environmentally friendly technologies. The logistics centre is used to hold textiles for forwarding to the company’s branch offices. The depot serves as a central logistics facility for all the group’s companies.
In the past, Peek & Cloppenburg used cardboard for packing apparel. But this approach had numerous disadvantages. Cardboard were not ideally suited to handling in the automated small parts store and on the conveyors. The unpacking, order filling and repacking of closed cartons required a considerable amount of manual handling. Furthermore, humidity made stable stacking problematic, while a huge amount of space was taken up by empty cardboard packaging. Peek & Cloppenburg also wanted to reduce packaging waste with a multi-way system.
Optimised supply chain
Schoeller Allibert’s technicians ran a thorough analysis of the situation on site as the basis for the new proposal. The cardboard were replaced by 45,000 plastic stack&nest crates. The boxes have a perforated bottom to allow extinguisher water to drain out freely, if necessary. This means that they are fully compliant with fire regulations for logistics centres. The stack&nest boxes have satisfied all the client’s requirements. The plastic containers are ideally suited to the automated small parts store, and they are easy to handle, whether automatically or manually, on the conveyors. Their low weight and ergonomic handles make them easy to use, and they are also hygienic. What is more, they need not be opened and closed – a considerable time saving. The containers do not need lids to protect against dirt, since the textiles are shrink wrapped.
And the stack&nest principle drastically reduces the space taken up by empty containers: empty boxes can be rotated 180° horizontally and nested inside each other – resulting in a 70% space saving. Peek & Cloppenburg now have more available space in their logistics centre and faster turnaround thanks to space-saving recirculation. The full boxes are both easy and very stable to stack, due to their load-bearing construction. The containers feature a two colour design to facilitate handling. The two colours make the workspace orderly and easy to monitor, since one can see at a glance whether bins are stacked inside or on top of each other. Deliveries to branch offices on pallets and cage trolleys have also been simplified, since the boxes come in standard sizes to make them compatible with all types of transport.
The environment also benefits
The changeover to stack&nest containers has also enabled Peek & Cloppenburg to make an important contribution to conserving resources. The very long-lived returnable plastic boxes have done away with the previous large volume of packaging waste. Carsten Scheer, director of the Peek & Cloppenburg Reinbeck logistics centre sums it up: “Schoeller Allibert’s packaging solution has made our processes much more efficient and is also saving us money. We have already recovered the initial investment.” The Peek & Cloppenburg KG group, with head offices in Hamburg, is the parent concern for VAN GRAAF and Peek & Cloppenburg. Both companies have operations in a variety of markets. Peek & Cloppenburg has 25 branch offices in 20 cities in Germany, making it one of the biggest family clothing retailers. VAN GRAAF, with head offices in Vienna, has operations in Poland, the Czech Republic, Hungary, Austria and Switzerland, and also operates a webstore for the German market. (www.vangraaf.com)