Say cheese! (and think Schoeller Allibert)
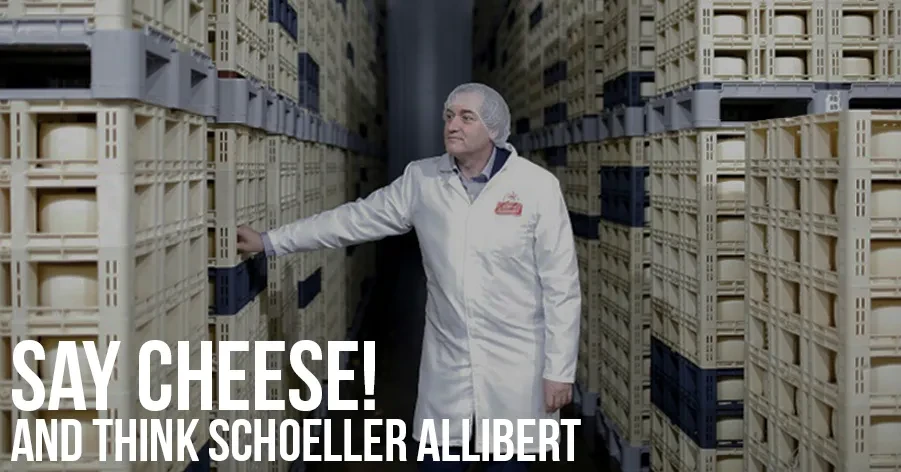
Contact us
Get in touchSchoeller Allibert is a champion provider of reusable and tough cheese (and dairy) packaging and assorted services. These increase the operating speed and energy efficiency of its customers’ businesses, while also reducing cost and environmental impact, and benefitting hygiene and safety. But don’t just take our word for it. Here we present you with eight customer testimonials, each highlighting a specific need, all met and surpassed by our products.
Cheese comes in all sorts, shapes and tastes. In terms of processing, ripening and storing, it’s a notoriously difficult product category to get right. Yet that is exactly what Schoeller Allibert has done. In 1970, we introduced a range of plastic containers for cheese, that has since evolved into a comprehensive logistics solution for the entire cheese industry – as well as the wider dairy sector.
After all these years, our products retain their innovative edge. Traditionally, cheese was stored and matured in single-use packaging. But the industry has come to realise that a more eco-friendly solution is possible: reusable packaging that retains the shape and quality of the cheese throughout the entire manufacturing process. Like the product range that we offer, and keep perfecting.
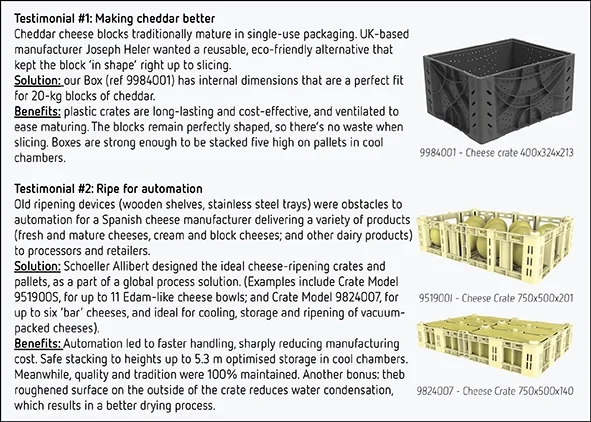
Schoeller Allibert has developed a range of boxes, intermediate bulk containers (IBCs) and foldable large containers (FLCs) to deal with all kinds of cheese – whether made from cow, sheep or goat milk; soft or hard; round, cylindrical, square or ball-shaped.
Our plastic cheese crates are all lightweight and strong, silent and 100% food-safe, and ideal for automating processes, from processing and storage to maturing and transporting. Maturing is the essential part of the cheese production process. That’s why our crates are fully ventilated, allowing the cheese to ripen naturally.
Next to our standard range, we offer tailor-made trays for specialty cheeses. The result: a complete set of solutions for the whole supply chain, from foldable IBCs over clean-room pallets to tailor-made ripening crates. And not just for the cheese industry but for the entire dairy sector. Our products have a maximised service life, helping our customers move towards the circular economy – and helping them to increase their profitability along the way.
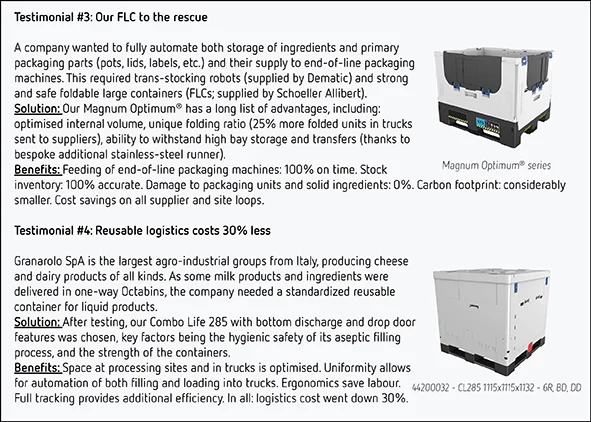
Our comprehensive offering includes products for:
Ingredients and packaging supply
(IBCs for liquid eggs, liquid and powdered milk, cream, yoghurt, etc.; and FLCs for packaging supplies such as caps and closures).
Processing
(cheese crates for food processing, Maxinest and other stack nest crates for retail, and automation-friendly pallets, to be used with cheese crates etc.)
Waste management
(Maxilog, Big Box Classic and other reusable plastic containers).
Our cheese crates are made to withstand long-term storage in cool chambers and are ready to be used in fully-automated warehouses. Using cheese crates from Schoeller Allibert means the cheese remains perfectly shaped and is perfectly matured, right up to the moment when it’s ready to be sliced.
Here are some specific qualities and advantages of our cheese crates:
Turning the cheese.
Cheese that’s maturing needs to be turned. Multiple pallet plus container solutions is uniquely designed to automatically turn up to 650 kg of cheese in one go.
Anti mould, pro bacteria.
Our crates are made from 100% food-approved plastic, which prevents the formation of mould (unlike wood or steel crates) – but does keep the bacteria essential for cheese maturing alive.
Rounded for easier cleaning.
Our crates are designed with rounded and slanted edges, making them easier and faster to clean.
All shapes and sizes.
Our crates are available in a wide variety of internal layouts, accommodating cheeses of all shapes and sizes.
Our IBCs, meanwhile, are also perfectly suited for liquid ingredients such as milk and eggs. Some specifics:
Bag in box concept
Using one-way liner bags in returnable IBCs help reduce packaging cost.
Hygienic and aseptic.
Designed and guaranteed to handle the highest quality of customer product.
Strong and repairable
Long lifetime and low maintenance cost enhanced by the fact that all parts can be replaced individually.
Tamper-evident and adaptable
Sealing can be provided, so tampering with content is impossible without visual evidence. A variety of liner bags, spouts, external connectors and valves is available.
Ergonomic
A drop door in our Combo Life 285 and Combo Excelsior® Hybrid enables easy access if needed.
Double savings
Save on one-way packaging by using this reusable solution, and on return freight and storage thanks to its foldable design.
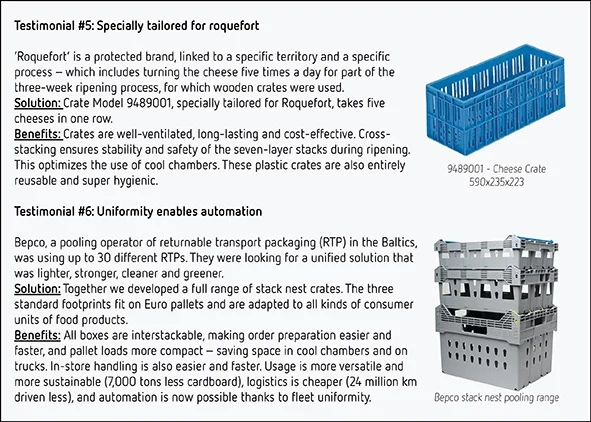
The food industry in particular is an economic activity where tradition and innovation go hand in hand to produce increasingly better results. One recent Schoeller Allibert innovation can be an important lever to improve quality, efficiency and, ultimately, revenue.
We’re talking about SmartLink®, a platform and suite of services introduced in 2021, built on track-and-trace technology embedded in the logistical product itself. Via our dedicated, secure and cloud-based SmartLink® platform, this technology provides real-time data on the movements and location of the assets. With so-called geofencing, operators can be alerted when assets enter or exit certain areas. But there’s more: the tracking devices can measure and transmit information on the temperature, humidity and fill level of the crates. Additionally, operators can add enterprise resource planning (ERP) data, linking product to content, thus providing insight in remaining shelf life.
In short: if your company is involved in any way in the logistics of producing, maturing, storing and/or transporting cheese and dairy products, Schoeller Allibert has solutions available – standard off the rack or tailored to your specific needs – that will help you be more efficient, automated and profitable.
Whenever you say cheese, think… Schoeller Allibert!
Contact us
Get in touchContact us
Inspiration
Related
Est proident veniam laborum exercitation est veniam reprehenderit nostrud officia. Ad Lorem aliquip duis labore duis. Irure deserunt eu minim culpa eiusmod quis ut sint eu pariatur magna aliquip et incidid voluptate cillum Lorem amet ea.
Navigating EU Sustainability Regulations in Transport Packaging—A Roadmap for Compliance and Opportunity
We’re thrilled to introduce our latest whitepaper: New EU sustainability regulations and their impact on packaging. Designed as your essential resource, this whitepaper breaks down the complex, changing landscape of EU s...
Read newsBepco Equipment Pooling system
Looking for rational logistics solutions to reduce damage to food products, improve order preparation speed and optimize truck filling along with an increased profitability for their own customers, Bepco pooling in the B...
Read moreSchoeller Allibert JumboNest® RTP Solution Shortlisted In UK Packaging Awards
Schoeller Allibert, the European market leader in the production of recyclable, reusable and returnable transit packaging (RTP), is celebrating the shortlisting of its newly launched JumboNest® returnable packaging solut...
Read news