The secret ingredient for summer food fun? Schoeller Allibert!
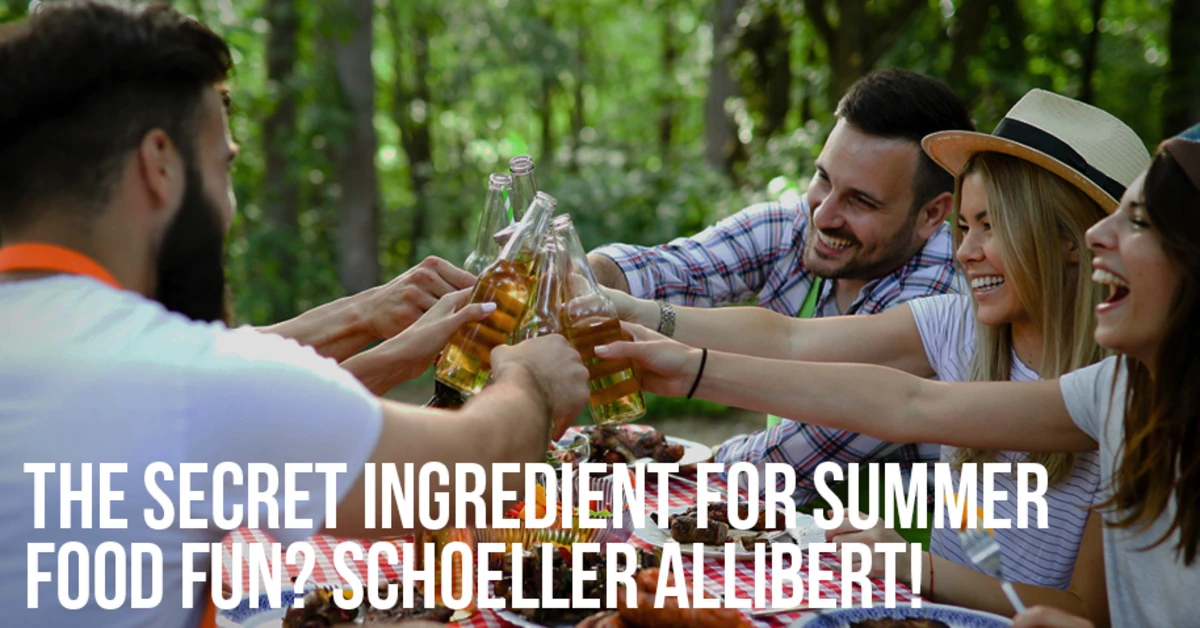
Contact us
Get in touchA family picnic here, a barbecue with friends there, and lots of open-air dinner parties in between: summer is the time when good food and good fun go best together. Getting all those delicacies – fruits and juices, meats and sauces, and much, much more – from field and factory onto your table (or picnic blanket) is a complex business. At Schoeller Allibert, we take pride in our role providing packaging and logistics solutions to the food and food processing industries. Think of us as a secret, yet essential ingredient for all your summer food fun!
It sounds like a paradox, but it’s true: when it comes to food packaging, Schoeller Allibert has a long history of innovation. Going all the way back to 1959, when Alexander Schoeller created the world’s first plastic beer crate.
Efficiency, savings and hygiene
Ever since, we’ve partnered with our industry customers to develop packaging solutions that bring efficiency, savings and hygiene to this very demanding sector.
Very demanding indeed, because the needs in the food and food processing industries are many, and the requirements are strict. Food must be picked, transported, stored and prepared before it ends up in the shop, and on your plate.
Depending on the type of food, it must stay fresh or ripen, be cooked or blast-frozen. Or used as an ingredient in another food product. All this in a logistics ecosystem that requires both high speed and strict hygiene, and that needs to be both highly automated and extremely flexible.
Complete range, improved handling
Thanks to decades of experience responding to industry needs and requirements, Schoeller Allibert offers a complete range of boxes, pallets, pallet boxes, large folding containers and dollies for improved handling of meat, poultry, fish, milk and dairy products, bread and confectionery, fruits and vegetables, and more.
Improved handling? Yes, because our solutions accelerate supply chain loops, and speed up processes – increasing profitability. Because our plastic packaging is not only hygienic, easy to operate and easy to clean, but also sustainable and, at the end of its useful life, fully recyclable. As we like to say: we make plastic that’s too good to waste!
And that’s not just a slogan. Our designers and engineers put a lot of thought and effort in designing packaging that’s just right for its purpose.
Sauce transport – and more!
Here’s a selection from our wide range of unique, reusable food packaging solutions:
Combo Fructus®. an intermediate bulk container (IBC) designed to transport tomato paste, fruit juices and similar. Challenges: long-range logistics, long-term storage. Solution: a range of safe, strong, clean and labour-saving IBCs available in three heights.
Combo Excelsior®. A foldable hygienic IBC ideally suited for long-range intercontinental logistics of all liquid food products. Very popular for transport of sauces, and saves space when empty.
JumboNest®. The first-ever 500L stack/nest RPC, capable of improving return logistics when empty.This one-piece design with smooth walls and drainage holes, making it easy to remove liquids and contaminants. Made from food-grade HDPE material that performs optimally under chilled conditions. Ideal for the meat industry.
H1 pallet. Hygienic, standard and safe. Strong, lightweight, rackable and suitable for automated handling. Fully compliant with the GS1 norm. Perfect for all fresh product logistics.
Maximeat 800x600. The efficient, lightweight and cost-saving alternative to existing roll cages. Suited for delivering raw or vacuum-packed meat cuts to stores. ?
Bread crates. Stackable, nestable, lightweight, easy to handle and highly ventilated to keep bakery goods fresh. (Our Broban crate is the preferred solution of many bakeries in the Benelux countries).
Fish boxes. Like the plastic beer crate, another of our earliest market-altering improvements. And we’ve kept innovating and improving since 1959. In our current model, drain holes get rid of excess meltwater, so the freshly-caught fish remains perfectly fresh.
Confectionery trays. Specifically designed to protect fragile products like cakes, pastries and savoury goods.Rounded angles make it easy to clean and won’t damage the content.
Cheese pallet and crates. Perfectly suitable for automated handling, unlike many other ripening devices. Plastic crates – compared to steel and wood alternatives - prevents mould, but preserves useful bacteria. Cheese-friendly design with rounded ribs allows the boxes to be turned without damage to the product. One more advantage: the roughened surface on the outside of the crate reduces water condensation, which results in a better drying process.
Beer crates. Designed to be ergonomical and ecological – in other words: easy to handle and good for the planet. That’s two more reasons for fun, as you use these crates to carry some fresh drinks to your party!
Forward-looking technologies
Schoeller Allibert’s offering to the food and food processing industries doesn’t just consist of various types of packaging, each ideal for specific types of food products and usage cases. We also offer a range of forward-looking technologies that help our customers proactively manage their logistics processes, uphold compliance and food safety. Saving time and money, and improving product quality. All of which ultimately benefits everyone along the value chain –producer, consumer, and everyone in between.
Which technologies? These three:
SmartLink®. Assets with Smartlink® have an in-built sensor, offering actionable supply chain insights. This information is extremely useful for tracking the freshness of the product, and the location (and progress) of the assets it’s being transported in. Temperature sensors inside the box make sure the cold chain doesn’t get interrupted.
Purity line. Responding to a growing awareness of health and safety issues in the market, we developed a range of fully recyclable products made from antibacterial materials that inhibit the growth of up to 99.99% of bacteria and moulds, for every step of the supply chain. For example, the Purity line has been proven to offer total protection against the E. coli and S. aureus bacteria.
Detectables. A range made from detectable materials, which enables customers to detect even very small particles in any food mix, via X-ray or metal scanners, thus ensuring food won’t get contaminated with foreign bodies.
Together with our engineers and designers, and of course also with our customers in the food and food processing industries, Schoeller Allibert will continue to work tirelessly to bring innovation to food packaging and logistics, improving quality and efficiency, productivity and profitability.
It’s hard work, but for us, that perfect barbecue, picnic and dinner is reward enough. We’re happy remaining the secret ingredient in your summer food fun.
Contact us
Get in touchContact us
Inspiration
Related
relevantItems.news.intro
Navigating EU Sustainability Regulations in Transport Packaging—A Roadmap for Compliance and Opportunity
We’re thrilled to introduce our latest whitepaper: New EU sustainability regulations and their impact on packaging. Designed as your essential resource, this whitepaper breaks down the complex, changing landscape of EU s...
Read newsIPL merges with Schoeller Allibert to create US$1.4 billion revenue reusable plastic packaging company
IPL, a manufacturer of rigid-plastic products, announced it is merging with Schoeller Allibert, a manufacturer of reusable transport packaging. The proposed merger creates an international sustainable packaging producer ...
Read newsSchoeller Allibert contributes in the global battle against COVID-19 with CG Chemikalien GmbH & Co. KG
When scientists began seeking a vaccine in early 2020, they were very careful in communicating a possible delivery date. The development of a vaccine is something that cannot be rushed and the fastest any vaccine had pre...
Read news