Magnum Optimum Hopper® 1208, dispensing excellence for the beverage industry
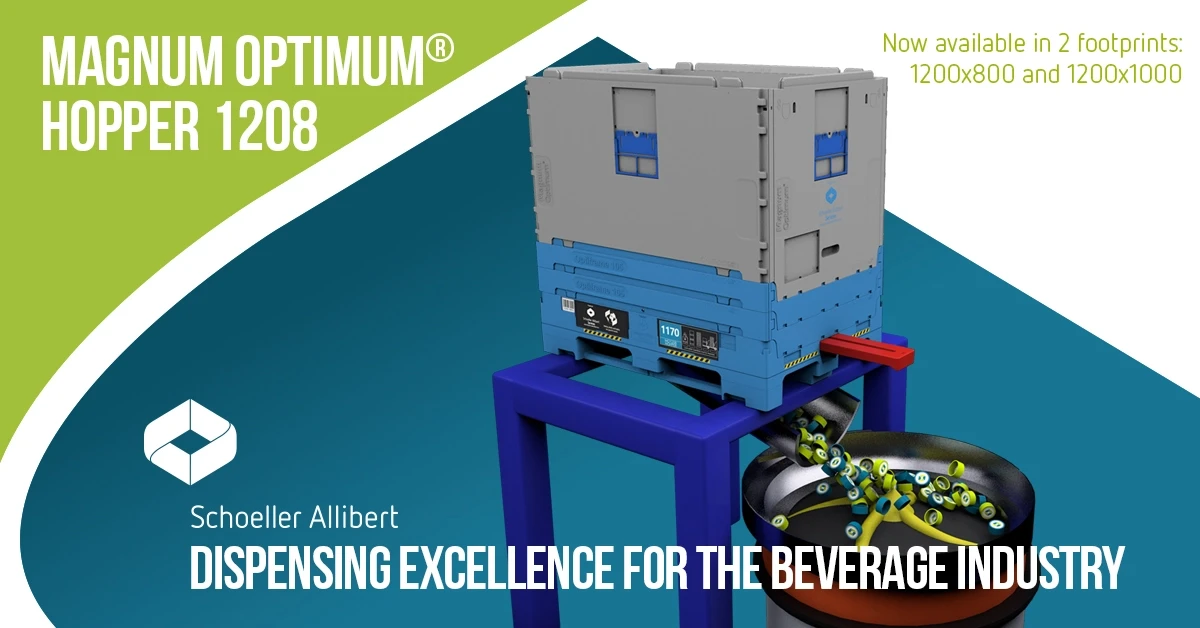
Contact us
Get in touchSchoeller Allibert developed approximately 20 years ago the new foldable format, which has become a global standard in many sectors. Following the successful introduction of the Magnum Optimum Optishute® and Magnum Optimum Hopper®, both with a standard footprint of 1200 mm x 1000 mm it was time to also introduce a 1200 mm x 800 mm footprint version of the Magnum Optimum Hopper®.
“The Magnum Optimum® range has already changed supply chains for a multitude of sectors. We are excited to share that Schoeller Allibert’s strongest Foldable Large Container (FLC) series will get another addition specifically for the beverage industry to dispense caps & closures in the most efficient way, the Magnum Optimum Hopper® 1208 .” Jan De Witte, CSO Schoeller Allibert Group.
The foldable, smooth foldable large container with hopper feature, is capable of dispensing parts through a base opening. This container will be the benchmark when shipping caps & closures for the beverage industry. Other than the beverage industry the Magnum Optimum Hopper® 1208 is extremely suitable for applications concerning food & food processing (like bubble gum, coffee cups, confectionary), dry chemicals, packaging (preforms) and raw materials (big bags) but can also be used in several other markets.
If you add our new service model to this, you will be able to easily rent this solution and track it through the SmartLink® platform. This will not only improve your supply chains’ KPI, but also will optimise your capex.
There is no need to wait to decarbonize supply chains Interested in renting. Contact us >>
Reduce your carbon footprint and eliminate packaging waste
With a weight of 71 kg and a usable volume of 725 litres the Magnum Optimum Hopper® 1208 can handle a unit load up to 500 kg. When empty it can save up to 57% of space, which means that in a standard trailer 66 erected boxed can be transported, while 165 units can be returned folded in the same standard trailer. This dramatically helps to reduce your carbon footprint by saving space in return logistics.
The Magnum Optimum Hopper® features a special hopper base which eliminates packaging waste and removes the need for liners, a separate pallet base or cardboard frames. The wide opening in the hopper base (286 x 186 mm) enables 100% control on the flow of all types of parts - including caps, closures, and accessories – meaning that they can be unloaded in evenly dispensed volumes and fully controlled quantities. In comparison with our Magnum Optimum 1210 Hopper® version, the dispensing slider is placed at the short side.
Need to dispense even more? The Optiframe® spacer increases the height and the volume.
Folding & unfolding in 5 seconds
Non-sequential folding and easy-to-handle sidewall locks make it possible for one operator to erect the container within 5 seconds. Thanks to the handgrips in the panels folding can be done within the same 5 seconds. The large self-locking drop doors on front and side combines easy operator access while maintaining the panel strength.
Anti-slip plugs reinforce safety and speed handling and fork tine guides on base, strong three skids base. Moreover a 4-way fork truckload entry and an easy to clean surface makes the Magnum Optimum Hopper® 1208 a must have product for all beverage supply chains.
Smooth as a …
The drainage holes of the Magnum Optimum Hopper® 1208 protect from retaining water if stored outside, its smooth walls and internal base are easy-to-clean and minimize cost of washing and drying.
Repairable, Reusable, 100% Recyclable
100% rackable and designed with standard sized panels and using Schoeller Allibert’s exclusive Bayonet® interlocking system. The Magnum Optimum Hopper® 1208 is reusable and sustainable: with a minimized number of parts that can all be easily replaced; maintenance costs are reduced, and life span increased. To further lower the carbon footprint the Magnum Optimum Hopper® 1208 can be fully recycled after its long service life.
Futureproof
Like the Magnum Optimum® 1208, the Magnum Optimum Hopper® 1208 also offers many identification options:
recessed zones for bar code labels on all sides
large inserts for customer logo for an easy identification of the fleet
pockets in skids are included for RFID labels or IoT (Internet of Things) devices
the ID plate on base indicates height and handling instructions to enable efficient tracking and fleet management.
Thanks to SmartLink® readiness, we are prepared for the future of logistics. The ability to track and trace deliveries in real-time provides total visibility and highlights transportation pinch points promoting future best practices – helping save on fuel costs and reducing polluting CO2 emissions.
Configured for endurance
Fully configurable based on the following options:
Lid/dust cover
Label holder(s)
Short sidewall options
Long sidewall options
Optiframe(s)® (up to 3)
Base footprint options
Technical details include:
External measurements: 1200 mm x 800 mm x 1168 mm
Internal measurements: 1142 mm x 742 mm x 987 mm
Weight: 71 kg
Capacity: 725 L
Unit load: 500 kg
Static stacked load: 2300 kg
Folding ratio: 57%
Folding height: 525 mm
Temperature range: -20°c to 40°c
Different configurations are possible.
Watch the video introduction of the Magnum Optimum Hopper®1208 here:
Contact us
Get in touchContact us
Inspiration
Related
Est proident veniam laborum exercitation est veniam reprehenderit nostrud officia. Ad Lorem aliquip duis labore duis. Irure deserunt eu minim culpa eiusmod quis ut sint eu pariatur magna aliquip et incidid voluptate cillum Lorem amet ea.
Navigating EU Sustainability Regulations in Transport Packaging—A Roadmap for Compliance and Opportunity
We’re thrilled to introduce our latest whitepaper: New EU sustainability regulations and their impact on packaging. Designed as your essential resource, this whitepaper breaks down the complex, changing landscape of EU s...
Read newsCase study: SVENSKA
The Swedish pooling company has chosen Schoeller Allibert Maxinext + for fruit & vegetables, meet and fish supply chain.
Read moreClient Application: COOPERL Arc Atlantique
Cooperl is one of the top pork meat processing companies in Europe. With 15 slaughtering and processing sites, Cooperl employs 4,800 people and revenue is more than 2 Billion Euros.
Read more