Gestamp Umformtechnik adopts the Magnum Optimum for inbound and internal logistics
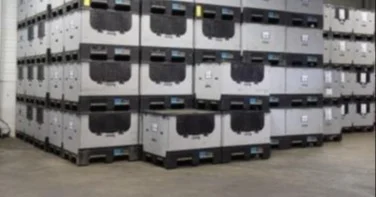
Industry
Contact us
Get in touchGestamp is one of the leading automotive suppliers worldwide. Specializing in steel parts and components, the Bielefeld plant needed to streamline the logistics of steel hollow frames supplied from Manchester in steel cages.
More space, less costs, better protection
Automotive supplier benefits from new transport containers
Gestamp Umformtechnik has brought the internal logistics processes ´to shape´. For the shipping and storage of body and chassis components for the automotive industry, plastic containers are now used by Schoeller Allibert. The large load carriers Magnum Optimum are a significantly more efficient packaging solution than the steel cages previously used for the application. The successful model should therefore be extended.
Gestamp is one of the top automotive suppliers worldwide. The company develops and manufactures steel bodywork, chassis and mechanical components for the international automotive industry. With about 1450 employees, the plant in Bielefeld is the largest production site of the Gestamp Group. On the business premises of approx. 200,000 m², a lot of activities are always running and the internal logistics areas are often busy up to the capacity limit. For a quick and easy storage and relocation of the goods, a cross-company planning and good ideas are needed. A smart solution was found for the shipping and storage of steel hollow frame. The curved frames with length of about 850 mm are produced in an affiliate company of Gestamp in Manchester, England and are delivered to Bielefeld for further processing for integral framework for wishbones.
Until 2015, Gestamp Umformtechnik packed the components in steel cages with dimensions 1240 x 835 mm. The temporary storage in the rigid steel cages however needed a lot of space and at the same time the empty transport to England caused high costs. Furthermore, an improvement in the field of product protection was needed, because the hollow steel frames were exposed in the open and unprotected outdoor storage in the weather, so that corrosion occurred.
Unnecessary empties reduced
Schoeller Allibert brought a remedy with a better alternative to the steel cages: the Magnum Optimum plastic container with dimensions 1200 x 1000 x 975 mm. As a unique load carrier available on the market, the transport packaging is certified with 750 kg load capacity and thus similarly stable as a pallet cage, but thanks to its lower weight, much easier to deal with. With Magnum Optimum, Gestamp Umformtechnik could permanently reduce the unnecessary empties by storage and delivery to less than one-third of the previous volume. Valuable place was won in the Bielefeld facility and the costs of the empty transport to England dropped significantly. With each truck now 208 folded containers could be transported and the number of empty trips has been highly reduced.
More products on the truck
Another important advantage of the new packaging solution is the larger capacity of the robust plastic container. 78 steel hollow frame could be transported with the cages, but Magnum Optimum offers enough space for 98 pieces. Gestamp Umformtechnik would transport earlier 60 steel boxes or 4680 steel hollow frames with one truck, now there are 52 plastic containers with 5096 pieces of content. In addition, dirt and rust on the components can be avoided from now on. The Magnum Optimum containers guarantee a good dust protection thanks to the closed side walls and the lid. The outdoor storage is also easily possible with them, because the drainage holes in the closed ground of the Schoeller Allibert packaging provide additional protection against wetness.
The handling of the long-lasting reusable containers is very convenient. The containers can be built and disassembled at lightning speed, without having to keep a particular folding order. The locks are easy and smooth surfaces facilitate the cleaning and reduce the risk of injury. Magnum Optimum also scores with greater flexibility comparing to other pallet cages. If Gestamp Umformtechnik wants to use the packaging for other products, it can be adapted in height anytime with the help of the attachable Optiframe frame.
Amortisation in less than one year
Frank Brindöpke, director of the Logistic Planning for the Gestamp Forming Technology, gives a verdict: "The packaging solution by Schoeller Allibert has made our logistics processes more efficient and saves a lot of money. The payback period of investment is less than one year." Within the next two years other suppliers of the Bielefeld production facility are expected to convert into the new packaging solution. An extension of the reference project on other sites of the Gestamp Group is also possible.
The Gestamp Umformtechnik GmbH belongs to the Spanish Gestamp Group with its headquarters in Madrid. The automotive supplier employs around 33,000 employees in over 90 locations worldwide. Gestamp Umformtechnik develops and manufactures high quality bodyworks and chassis components for the international automotive and commercial vehicle industry in its two sites in Bielefeld and Ludwigsfelde. There are Gestamp Umformtechnik components in almost every European vehicle: from the sliding door on the B-pillars to the rear axle. The most important customers include international car manufacturers such as BMW, Daimler, Ford, Volvo and VW, as well as the agricultural machinery manufacturer John Deere. (www.gestampumformtechnik.de) Schoeller Allibert is the worldwide market leader in reusable packaging made of plastic for transport and storage. For more than 60 years, the company has optimised the supply chains and reduced logistics costs of his customers. Typical areas of application areas of the packaging solutions are the areas of agriculture, automotive industry, retail, food and beverage industry, manufacturing as well as pooling services (www.schoellerallibert.de)
Industry
Contact us
Get in touchContact us
Inspiration
Related
Est proident veniam laborum exercitation est veniam reprehenderit nostrud officia. Ad Lorem aliquip duis labore duis. Irure deserunt eu minim culpa eiusmod quis ut sint eu pariatur magna aliquip et incidid voluptate cillum Lorem amet ea.
Navigating EU Sustainability Regulations in Transport Packaging—A Roadmap for Compliance and Opportunity
We’re thrilled to introduce our latest whitepaper: New EU sustainability regulations and their impact on packaging. Designed as your essential resource, this whitepaper breaks down the complex, changing landscape of EU s...
Read newsFoldable pallet containers at Continental
CONTINENTAL Automotive Czech Republic s r o, located in Turnov, is manufacturing and assembling pumps and engines modules for major OEM vehicles companies worldwide.
Read moreMagna Steyr BMW Group
The BMW Group signed an agreement with car producer Magna Steyr covering the development and production of the new BMW X3. Never before had an automobile manufacturer assigned such a large-scale project to a single partn...
Read more