Thinking inside the box: How smart food packaging does your work for you
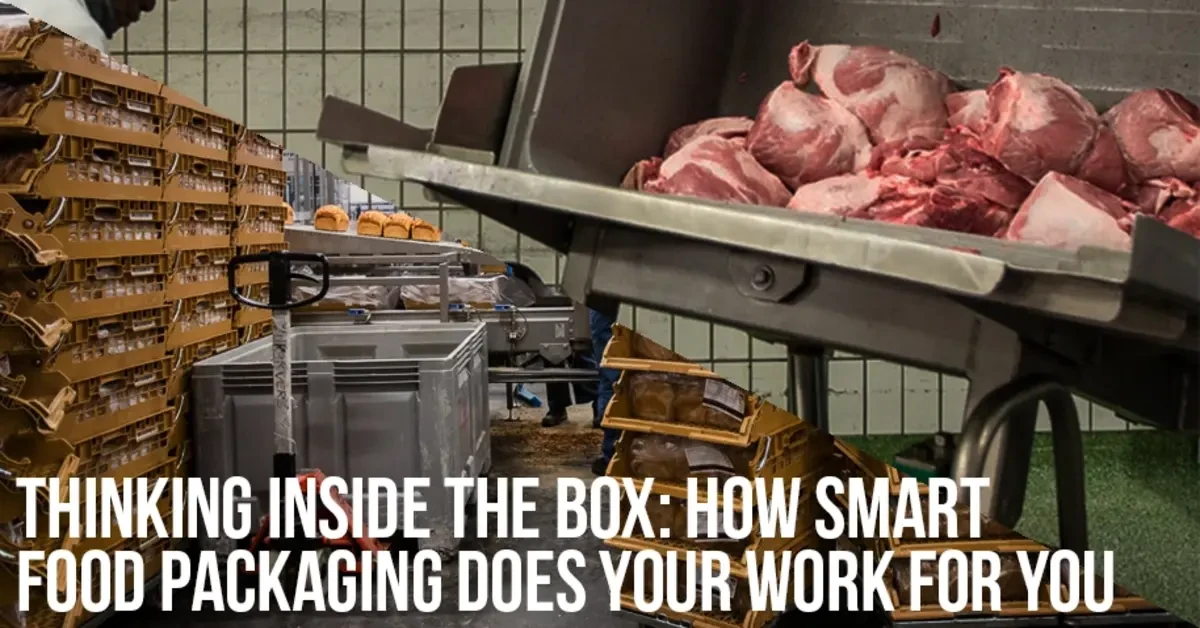
Contact us
Get in touchFood companies demand returnable transit packaging (RTP) of the highest quality – and rightly so. But these days, they can get more out of their RTP than ever before. In fact, they can get their food packaging to do their work for them. Smart packaging can be tracked and traced – and even keep you updated about its temperature and fill level. Call it “thinking inside the box”. It’s the future of food packaging.
RTP in the food and food processing industries must withstand a wide range of harsh conditions: from blast freezing and steam cooking to industrial cleaning. Schoeller Allibert’s Rental division offers RTP for a wide range of applications, made from reusable plastic that is designed and built to do just that.
More cost-efficient
But Schoeller Allibert goes above and beyond those targets. That’s how we keep ahead of the competition, and of our customers’ expectations. Food companies using Schoeller Allibert’s Rental products get more than an efficient, hygienic and cost-effective RTP solution. Via Smartlink®, you can also drastically improve your supply chain management.
So, what is Smartlink® exactly? Well, you’ve heard about thinking outside the box. This is thinking inside the box. Smartlink®-enabled RTP has a built-in sensor that allows you to track and trace it. The sensor does more than just transmit location: it also informs you about the RTP’s temperature, fill level and battery level, and it alerts you on geofencing issues.
All this data, which is accessible via Schoeller Allibert’s online Smartlink® platform, creates useful and actionable insights. Stay up to date on your crates’ location and movement. Get an alert when they’re not moving. Keep an eye on the temperature of your shipment, to maintain the quality of the content. And much more. Thanks to Smartlink®, your asset management will become more transparent, more proactive, more effective, and – thanks to all those improvements – also more cost-efficient.
Smartlink® can even enhance the safety and security of your process. Schoeller Allibert now offers Detectable HDPE and PP plastic materials, which fully guarantee the detection of small plastic and metal particles in any food mix – hence avoiding costly customer claims and/or reputational damage.
Highest quality demands
Smartlink® is a next-level innovation, but it is built on the solid foundation of decades of customer-focused improvement. Schoeller Allibert’s RTP is designed to meet all the practical needs and ensure the highest quality demands that their clients may have:
All products have standardised dimensions, for seamless process flow and logistical efficiency.
All products are designed to maximise the quality and preservation of the food products.
All products are designed to avoid dirt traps and ensure easy washing.
All products are certified for food contact and compliant with current EU and international food safety standards.
On top of all that, all Schoeller Allibert’s RTP for the food industry is made from plastic that is not only hygienic and durable enough to be used many times over, but that is also – at the end of its very long lifespan – recyclable. Which minimises environmental impact and maximises customer profit.
This point is important, but also somewhat counter-intuitive. So let’s explain: the best way to reduce the CO2 footprint and improve the sustainability of your food logistics is not to replace one-way plastic with cardboard packaging. Reusable plastic is more efficient, flexible, sustainable and – due to the high demand for cardboard – also better value for money.
No pollution, no waste
And Schoeller Allibert’s RTP is more than reusable. It’s also recyclabe. Via processes approved by the European Food Safety Authority in 2014, old RTP can be recycled into new RTP, creating a 100% sustainable packaging cycle. It’s a closed loop that supports Schoeller Allibert’s ambition to work towards a fully circular economy. In other words: no pollution, no waste! The accredited process covers both food-grade HDPE and PP crates. This reduces both the packaging cost and the carbon footprint of our customers.
You don’t develop such an intimate knowledge of customer needs overnight, nor indeed such an integrated approach to product design. Our history with food packaging goes back all the way to 1959, when Schoeller Allibert designed and produced the first-ever fish crate made from plastic.
This set in motion a rich tradition of innovation in food-related packaging products, ranging from ingredients supply all the way to retail shelves. Our focus: delivering greater efficiency, more savings and better hygiene to a highly demanding industry.
Smartlink® takes this innovative spirit to the next level – food packaging that’s not just ergonomic, cost-efficient, eco-friendly, easy to use and hygienic, but smart as well. That opens the door to even more gains in speed, cost and quality along the supply chain, benefitting not just food companies and their clients, but also the environment.
Services included
Schoeller Allibert is not just about the hardware. It comes with services included. Schoeller Allibert Services helps you track and connect with your Smartlink® assets, access the data they produce and act accordingly.
The result: improved cycle times and asset utilisation; fully automated, multi-location inventory registration; easy implementation of back-to-back hire fee invoicing; and more. In short, Schoeller Allibert Services helps you get over the digitisation hurdle and make the most out of the connected assets offered by Smartlink®.
And finally: here’s yet another reason why Smartlink® is so smart. Our customers rent the products instead of buying them. That reduces their capital spend, and increases their flexibility to upscale products and benefits when needed. Rental: the smartest way to get more bang for your buck!
The future of food packaging is here. It’s time to think inside the box.
Some of our featured products that will help you optimise your food supply chain:
Our JumboNest® is ideal for the fresh meat industry, and is 100% hygienic thanks to its monobloc design, smooth walls and top rim drainage holes. The Jumbonest® is the largest stackable and nestable rigid pallet container (RPC) on the market, optimizing vehicle fill when empty.
The Combo Excelsior Hybrid® is a bag-in-box Intermediate Bulk Container (IBC) solution for condiments, syrups, oils, etc. Its design is safe, easy to use and hygienic. This strong & hygienic box is the standard in folding IBC’s in the food market. Thanks to its Releasy® mechanism, valves can be fitted & removed easily.
The MaxiLog® is the all-rounder product, for transporting food or large-volume bulk such as pork loins, ingredients, etc. It’s strong, sturdy, automation-friendly, safe and easy to clean, and it’s designed especially for all needs of industrial processing and food production.
Our H1 pallet, the industry standard for the meat industry, is fully compliant with the GS1 norm. Both the pallet’s design and its performance meet the logistics needs for all fresh products: it’s strong, rackable, lightweight and suitable for automated handling
Contact us
Get in touchContact us
Inspiration
Related
Est proident veniam laborum exercitation est veniam reprehenderit nostrud officia. Ad Lorem aliquip duis labore duis. Irure deserunt eu minim culpa eiusmod quis ut sint eu pariatur magna aliquip et incidid voluptate cillum Lorem amet ea.
Navigating EU Sustainability Regulations in Transport Packaging—A Roadmap for Compliance and Opportunity
We’re thrilled to introduce our latest whitepaper: New EU sustainability regulations and their impact on packaging. Designed as your essential resource, this whitepaper breaks down the complex, changing landscape of EU s...
Read newsTetra Pak and Schoeller Allibert to launch transport crates made from used beverage cartons
Lausanne, Switzerland, 31
Read news