Field to fork, Schoeller Allibert knows how to handle your fruit
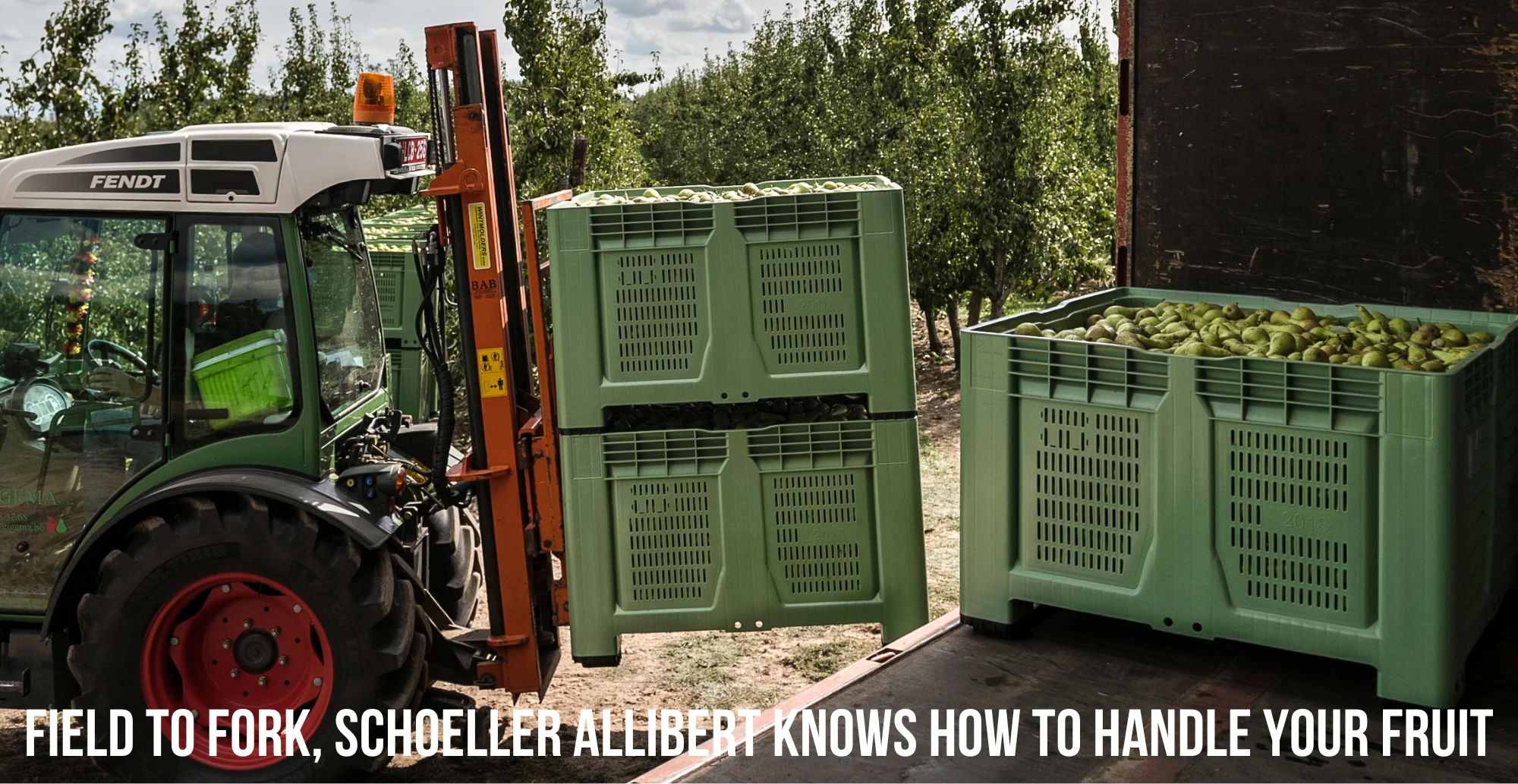
Contact us
Get in touchField to fork, Schoeller Allibert knows how to handle your fruit
Few product categories are as fragile as fruit. In other words: high-quality logistics can make the difference between delicious, high-revenue produce, and spoilt cargo that has lost its value. It’s a topic that gains urgency as harvest time approaches. Fortunately, Schoeller Allibert has a wide and specialised range of containers that are ideally suited to handle all kinds of fruit, all the way from field to fork.
Who doesn’t like raspberries or strawberries? Who wouldn’t appreciate some lovely peaches or prunes? Even if you prefer one over the other, you’ll agree that the best way to enjoy any kind of fruit is as fresh, crisp, and unbruised as possible.
Schoeller Allibert can help. In fact, we’ve been helping get fruit from field to fork in optimal condition for more than 40 years. In that time, we’ve gained lots of experience and expertise, which we’ve translated into a range of logistics containers that is as varied as the produce it carries, and designed to handle the various products in optimal condition.
Nothing complements experience and expertise as well as the ambition and drive of a new appointment, in this case: Jean-François Travers, newly minted as Schoeller Allibert’s Global Sales Director Food & Food Processing.
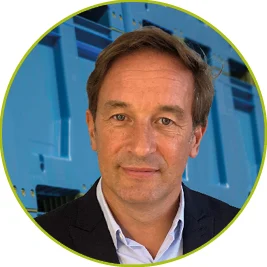
“In my new position, I want to play a leading role in ensuring that our solutions – current and future – make a crucial difference for our customers in meeting their CSR strategy. I’m convinced that the design of our solutions and their quality on a global level will be essential in improving the logistics for all players in the agriculture market.”
Case study 1
Bicolor crates: less volume, more sustainability
For decades, Dutch fruit growers H. Bloed used 40x30 wooden crates, each containing a maximum of 3 kg of berries, all with a maximum lifespan of 3 years.
Using Schoeller Allibert’s Bicolor Stack Nest crates (ref. 9703002), which can hold up to 5 kg each, H. Bloed was able to reduce the volume of crates in their supply chain from almost 7,000 to only 4,000.
Not only does that mean less packaging and less storage space needed, the plastic crates also have a much longer lifespan and are entirely recyclable into new crates - increasing the sustainability of the company’s logistics operation.
Added bonus: the smooth exterior of the crates offers branding opportunities for the company’s products.
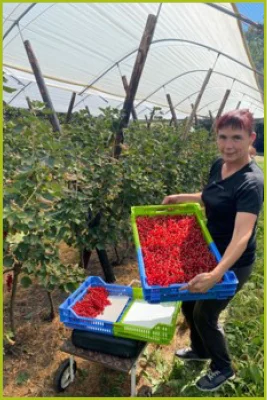
How are we going to do that? Here we present you with our main product categories that are suited for handling fruit, and some interesting customer stories detailing how Schoeller Allibert has made a positive difference in their operations, from harvesting and processing to transporting fruit in all its variety.
Our solutions for handling fragile fruit in optimal conditions come in three categories: rigid pallet containers (RPCs), space-saving containers, and SmartLink® and other RFID solutions. Let’s start with the RPCs, available in various size categories:
Low: Agrilog® (1200x1000x581 mm)
Specifically designed to preserve the quality of fruit (and vegetables).
Its pyramidal base structure reduces shocks while harvesting and helps to distribute the produce evenly.
Facilitates ventilation, drainage and cleaning.
Standard: AgriPlus (1200x100x780 mm), MaxAgri (1200x100x760 mm), and Maximus® (1200x1000x780 mm)
AgriPlus also features a pyramidal base for shock resistance and produce distribution, and an optional ventilation column to optimise airflow, enhancing the freshness of moisture-sensitive produce like garlic and onions.
Sturdy and highly ventilated, MaxAgri is designed for maximum internal volume, has four ‘pockets’ in the base to protect fruit and veg from damage and bruising, and is designed to withstand both extreme heat and cold.
The ideal ‘Big Box’ for fruit and veg, the Maximus® also features four pockets in the base to protect produce, and its convex walls help maximise internal volume, providing up to 20 litres more storage than comparable RPCs.
Case study 2
Big Box RPCs: saving €1.2 million each year
Spanish fruit processors SAT Guadex used small plastic containers to handle their growers’ asparagus, citrus and stone fruits.
Schoeller Allibert’s Big Box RPC (1200x1000x585), with its ventilated sides and base, anti-rolling design, and 500 kg unit load resistance, enabled the company to process larger volumes per container, without compromising on quality.
The Big Box’s bigger volume and stackable design improved storage capacity, and facilitated both transport and processing logistics. This RPC also enabled automated handling, which led to annual savings of €1.2 million.
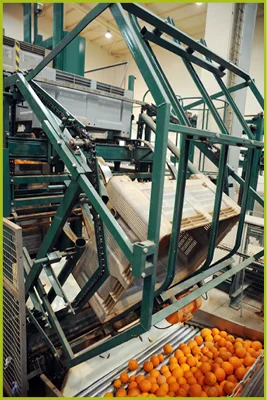
Large: Maximus® (1200x1200x790 mm)
With its slightly larger size, this is an even bigger box than the other Maximus®. Its entirely square footprint further facilitates large-volume logistics.
Like its smaller sibling, this Maximus® has rounded corners for easy cleaning and maximum hygiene, and can be stacked up to 10 high.
American: AgriMax (48x48 inch)
Ideal harvest and storage bin for the U.S. market, suitable for many kinds of fruit and veg.
Strong yet well ventilated, with airflow keeping produce fresh for longer while also offering faster drainage.
Optional: GPS tracking, barcoding, branding, and more.
Other specialised crates include:
Berry crates (400x300 mm, 500x300 mm and 600x400 mm footprints, in a variety of heights)
Specifically designed for harvesting, cooling and transporting soft fruit.
Ventilation and handling features specifically designed for optimal soft fruit and spices production.
Case study 3
Bicolor crates: 70% less storage space
Wine growers in France’s Bordeaux and Burgundy regions each used their own boxes to deliver their grape harvests. Because of different sizes, the boxes had no unified tare weight, were all handled manually, and took up more storage than strictly necessary.
By providing uniformity, Schoeller Allibert’s Bicolor Stack Nest crates offered a unique and constant tare weight, which made it easier for growers to measure their harvests. The lids protected grape quality. And the crates also facilitated automation, saving on labour cost. Last but not least, the crates’ advanced nesting capabilities saved 70% space on storage and return trips.
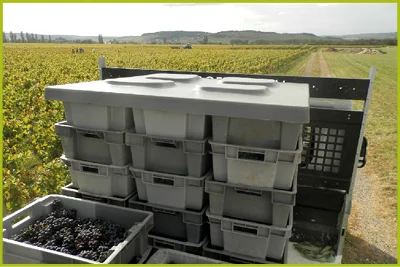
Champagne crates
Specially designed 30 years ago for harvesting the grapes used in the production of wine and champagne.
90-litre non-euro stacking container with ventilation holes on all four sides, to ensure evacuation of water and/or grape juice whilst reducing acidity.
PackPal® pallets (1200x800 mm and 1200x1000 mm footprints, in a variety of heights)
Versatile, lightweight and strong, can be used in all industries.
Pallets are used to transport fruit bins from the harvesting fields.
Versions with 9 feet can be nested when empty.
Versions with safety rim ensure that goods remain securely in place and provide stability when stacked.
All of Schoeller Allibert’s RPCs (except the AgriMax) can be made out of CircuLine® material. This means they contain recycled plastic, which helps reduce the need for virgin plastic. In so doing, CircuLine® products contribute to a more sustainable world – but without compromising on safety and quality. All conform to EFSA food safety requirements for fruits, vegetables, meat and packed foodstuffs.
Case study 4
Stack- and nestable plastic crates: eliminating moisture retention
Wooden crates, used by many stone fruit harvesters, appear sturdy and robust, but tend to absorb moisture which creates three important problems: the crates’ tare weight changes, the quality of the fruit is affected, and outside storage damages the crates.
Schoeller Allibert’s stack- and nestable plastic crates not only stack and nest at several heights (according to type of fruit), which ensures high-capacity storage and transport. They are also impervious to moisture retention. This prevents damage to the fruit and the crate itself, and ensures a constant tare weight; a triple win.
Next to RPCs, Schoeller Allibert also offers a range of popular space-saving solutions suited for handling fruit (and veg), and ideal for both harvesting and store display. These include:
Bi-colour Stack Nest crates (500x300 mm and 600x400 mm footprints, in a variety of heights)
This range of stack- and nestable containers offers nesting ratios from 50% to 80%, which greatly reduces reverse logistics costs.
The bi-colour design facilitates fast and safe handling.
Featuring strong, flat or reinforced bases, these crates are compatible with roboticised and automated handling.
Maxinest
Award-winning range of stackable and nestable containers, designed to replace one-way transport packaging for food and grocery retail.
The only produce tray offering multi-height options, which enables the same tray to be used for different applications.
Maxinest Plus conveyor base is suited for automated handling.
Textured surfaces allow for easy removal of adhesive labels.
Case study 5
Stack Nest 180: unique 80% nesting ratio
A cooperative received lettuce from over 1500 growers into 12 packing houses in 5 European countries in a variety of crates. That meant lots of manual labour, and lots of wasted storage space (also in trucks to and from the growers). The logistics issue was particularly wasteful in winter, when produce has to travel 500 km for processing.
Enter the Stack Nest 180 (ref. 8110720), a crate with a 40-litre capacity and a 10-kg load. With open handles for easy handling and smooth, rounded surfaces inside, it’s ideal for transporting something as delicate as lettuce. Plus, its ventilated walls and base create optimal airflow. Last but not least, its 9-on-1 stacking and its unique 80% nesting ratio optimise the available transport and storage space.
With all growers using the same box, automation is now possible, increasing efficiency and reducing cost.
Other crate models are available in various volumes, each ideally suited for different kinds of lettuce.
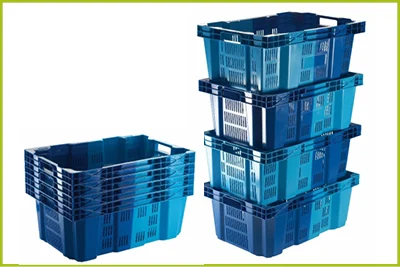
Prelog Classic & XLXS foldable crates (400x300 mm and 600x400 mm, in a variety of heights)
Both ranges are hygienic and well-ventilated foldable containers.
Well suited to protect produce from damage, from fields via distribution all the way to retail display.
High degree of foldability saves space on return trips or during storage.
Many of our products are compatible with SmartLink®, our in-house telematics solution that keeps you informed in real time of the location and movement of your container, and the condition of its cargo (notably temperature, humidity and fill level). This is invaluable information that will help you optimise your logistics flow, especially for products as fragile and sensitive to outside conditions as fruit and vegetables.
Long story short: Schoeller Allibert has a range of plastic containers, crates and intermediate bulk containers that offers sophisticated and standardised solutions for gathering and processing fruit and veg. Our products are sturdy, reusable, and ready for automation. This reduces cost and increases efficiency, providing a rapid return on investment.
Want to know how we can help you accomplish all of that? Contact us at info@schoellerallibert.com
Contact us
Get in touchContact us
Inspiration
Related
Est proident veniam laborum exercitation est veniam reprehenderit nostrud officia. Ad Lorem aliquip duis labore duis. Irure deserunt eu minim culpa eiusmod quis ut sint eu pariatur magna aliquip et incidid voluptate cillum Lorem amet ea.
Navigating EU Sustainability Regulations in Transport Packaging—A Roadmap for Compliance and Opportunity
We’re thrilled to introduce our latest whitepaper: New EU sustainability regulations and their impact on packaging. Designed as your essential resource, this whitepaper breaks down the complex, changing landscape of EU s...
Read newsAB InBev new Jupiler Orange Gold beer crate
World leader of beer industry with a production of 446 million Hectoliter production per year, AB Inbev has operations in 24 countries.
Read moreNew blow molding machine at the Winsford site
Schoeller Allibert has invested in a state of the art blow moulding machine to double its in-house production capacity for the Maxipac, in response to increasing demand for the folding bulk shipper.
Read news