Reducing our carbon footprint by a factor eight
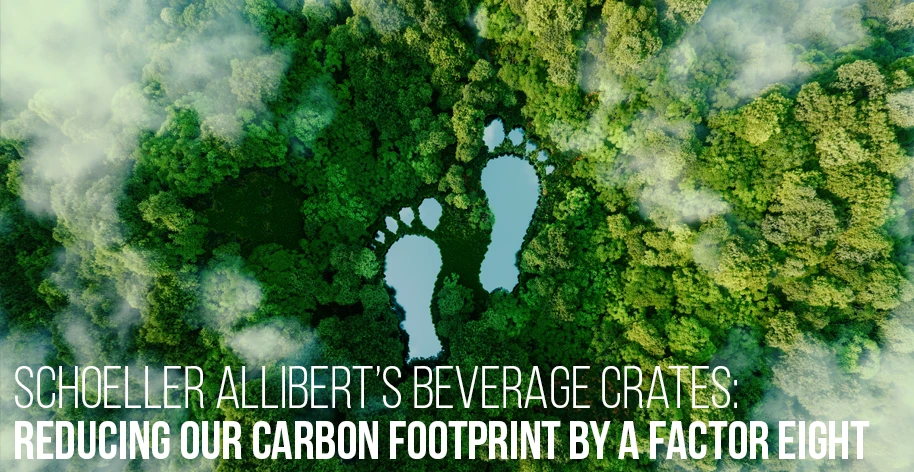
Contact us
Get in touchIn order to prevent climate disaster, the whole world is working hard to reduce its CO2 emissions as much as possible. Schoeller Allibert is leading by example. We have made exceptional strides in beverage crate recycling, successfully reducing our carbon footprint by a factor of eight. Here's how we achieved this.
While our beverage crates are highly reusable, lasting up to 30 years, and fully recyclable, the production process still generates CO2 emissions. To address this, Schoeller Allibert made the crucial decision to transition its production sites to renewable energy sources. The impact of this change was substantial.
To assess the magnitude of that achievement, we engaged ClimatePartner, an independent provider of climate action transparency. They conducted an evaluation using as standard reference a 1.9-kg bottle crate made from high-density polyethylene (HDPE). Here's what they found:
Manufacturing the 1.9 kg HDPE crate from virgin material in a conventional plant creates 5.9 kg of CO2-equivalent emissions. About three quarters of this total comes from obtaining, transporting, and processing the virgin material, while approximately 20% stems from ‘grey energy’ used during production. Logistics and other factors account for the remaining emissions.
By replacing the conventional grey energy with renewable green energy, the carbon footprint of a single HDPE crate is reduced by a full kilogram, resulting in just 4.9 kg of CO2 equivalent.
The largest contributor to the carbon footprint is the use of virgin materials. However, by practicing cradle-to-cradle recycling, with regrind levels of up to 95%, and utilizing renewable energy, the total carbon footprint for the HDPE crate plummets to a mere 0.7 kg. Logistics and general emissions constitute most of the remaining footprint.
In short, the same HDPE crate can now be produced with over 5 kg less CO2-equivalent emissions. What's more, Schoeller Allibert goes the extra mile by offering to offset any residual emissions, ensuring a fully certified and climate-neutral product for our clients.
CASE STUDY
Life cycle assessment: 60% less emissions
Every product has a carbon footprint. How do you measure it? The only right answer is to look at the product’s entire life cycle: from sourcing and processing the raw materials, over manufacturing and distributing the product, to its useful life and finally its end-of-life disposal.
In that holistic perspective, it’s only logical that returnable transport packaging has a very small footprint. Why? Because it is made of plastic that is strong, durable and easy to clean. It can be used over and over again - meeting strict food safety requirements.
And at the end of its life, it gets recycled into a new plastic container. And again. And again. Etcetera. Without loss of quality.
So, how does returnable plastic packaging stack up (pun intended) against disposable cardboard packaging? The renowned Fraunhofer Institute in Germany has done a life cycle assessment of both formats, and concluded that returnable plastic packaging generates around 60% less greenhouse gas emissions than disposable cardboard packaging.
That’s a feather we at Schoeller Allibert are more than happy to stick into our cap.

Contact us
Get in touchContact us
Inspiration
Related
Est proident veniam laborum exercitation est veniam reprehenderit nostrud officia. Ad Lorem aliquip duis labore duis. Irure deserunt eu minim culpa eiusmod quis ut sint eu pariatur magna aliquip et incidid voluptate cillum Lorem amet ea.
Navigating EU Sustainability Regulations in Transport Packaging—A Roadmap for Compliance and Opportunity
We’re thrilled to introduce our latest whitepaper: New EU sustainability regulations and their impact on packaging. Designed as your essential resource, this whitepaper breaks down the complex, changing landscape of EU s...
Read news5 great reasons to convert your single-use wooden pallets to durable high-performance plastic!
It’s never been more important for the commercial supply chain to up its game in terms of sustainability, transparency and performance – which makes it an ideal time to explore the advantages of durable plastic transit p...
Read newsImproving compliance on Li-Ion battery supply chain
Lithium batteries have become an essential component of many electronic devices, from smartphones and laptops to electric cars and renewable energy systems. However, ensuring the safety and reliability of lithium battery...
Read news