A crisis? Yes, but also an opportunity to improve your automotive logistics
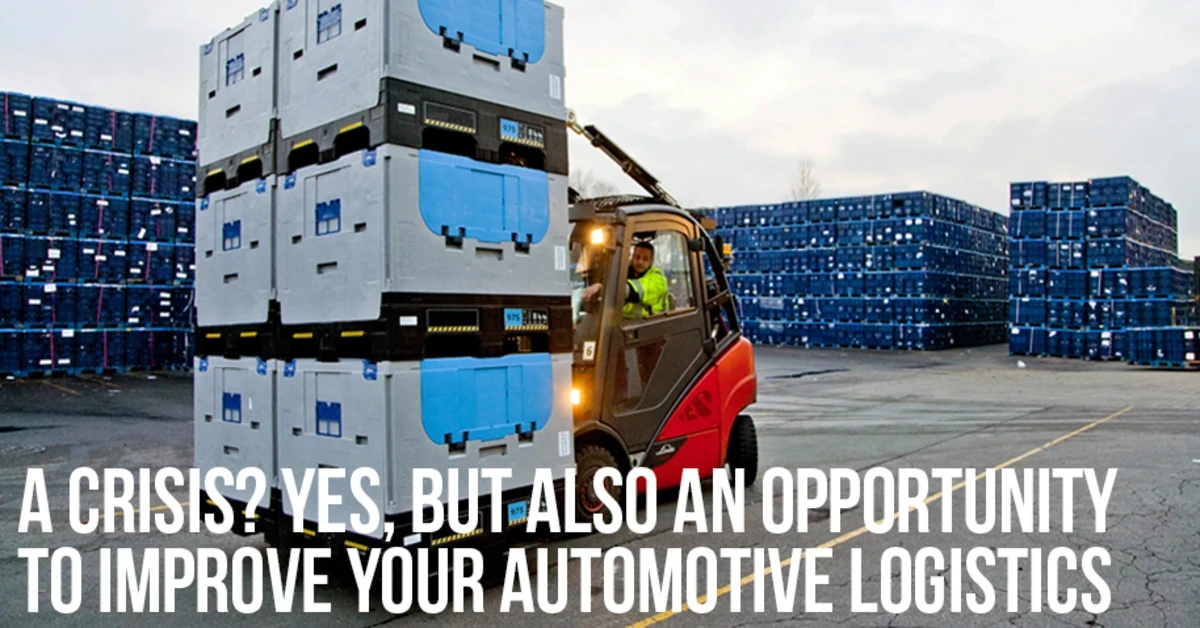
Contact us
Get in touchCrises, they say, are opportunities to do better. The automotive industry, which right now is undergoing significant supply chain disruptions, is a good example. This is an excellent time to review your automotive logistics. Schoeller Allibert has a range of solutions that will help you improve your operations, your efficiency and ultimately your profitability. That should sound like music to anyone’s ears!
There are new products to consider, but also new procurement options to evaluate. Let’s start with the rental option.
Especially in economically uncertain times, renting the assets you need has a number of advantages over purchasing them.
One: you don’t need to fork out a substantial down payment for the assets, and you pay more manageable monthly instalments instead.
Two: renting means you’re flexible. It’s easier to match the number of assets you have to the volume you actually need.
And three: you always get the newest, latest, top-of-the-line products.
Top of the line, we say? Yes: these products’ advantages are numerous, and will have a significant, positive impact on your bottom line. Which products? Well, the MO1208 and the RackPal, for instance!
MO1208 vs. Gitterbox
We all know the Gitterbox and what it can do. But tried and true is not always the best way forward. For one thing, the steel needed to make these containers is also in short supply – making this solution quite expensive. (The same goes for the nails that hold wooden pallets together, by the way).
It’s time to consider new methods and new products. Such as the Magnum Optimum®1208, for short: the MO1208, designed, manufactured and marketed by Schoeller Allibert.
Here are no less than 10 (yes, ten!) reasons why the MO1208 – certified to the DIN EN 13626 norm, by the way – is actually a lot better than the Gitterbox:
No corrosion. The MO1208 is 100% plastic.
Lighter. The MO1208 weighs at least 30% less than a Gitterbox. That translates into less fuel needed, i.e. lower transport cost.
Foldable. Up to 363 folded units fit into a single megatrailer. Less volume on return trips means, again, lower transport cost.
Easy to repair. Thanks to the Bayonet system, components can be easily replaced. Meaning repairs are simple, fast and low-cost, and can be done on-site.
Sturdy. Each MO1208 has a load capacity of up to 750 kg. That makes it ideal for transporting any type of automotive part.
Automation-friendly. The MO1208 is designed to be fully integrated into automated logistics processes.
Versatile. The MO1208 series is available in five base configurations, two wall configurations (solid sidewalls or with a drop door) and a variety of accessories (including lid, dust cover, and OptiFrame).
Dunnage. The OptiFrame (which increases the MO1208’s height by 105 mm per unit) is the ideal solution for dunnage (i.e. to ensure product protection during transport).
Track- and traceable. SmartLink’s embedded IoT devices offer full supply chain visibility, allowing customers to maximise efficiency and eliminate both idle time and losses.
Compatible. The MO1208 fits to all automated equipment developed for the Gitterbox as well as for a standard Euro pallet.
Obviously, such a broad range of qualities translates into an equally wide range of advantages. To bring home the difference with business as usual, let’s quantify just one example.
Say, your fleet has 2,500 containers, and they do 20 loops per annum. If instead of the Gitterbox you use the MO1208, you:
use 73% fewer trucks (because of better filling, and thanks to the foldable design, which reduces the number of return trips required),
and consequently also produce 73% less CO2 in return transport,
need 73% less time to load and unload the trucks with empties,
and require 73% less storage space for the assets (again, thanks to foldability).
RackPal® vs. wooden pallets
As if supply chains aren’t in enough trouble as it is, a pallet shortage threatens to further disrupt the flow of industry, including in automotive. Why not let this be the final push to switch to other solutions instead?
Take RackPal®, a plastic pallet solution that already boasts a good number of advantages over wooden pallets.
It doesn’t splinter, nor does it absorb water. So it’s cleaner. Because they’re plastic and hygienic, they’re exempt from ISPM 15.
There are no nails in the pallets. So they can’t damage goods or injure operators, and they last longer.
Heat-treated or fumigated pallets require all sorts of paperwork. These don’t. And the advantages don’t stop there. RackPal® 1208 is lightweight, rackable and strong – in other words, the ideal pallet for automated logistics.
It’s silent on conveyors, has optional anti-slip features and is designed to hold foil wraps and strap hooks to secure loads.
It’s available with various reinforced deck and safety rim options.
Depending on deck option, each RackPal® 1208 can hold from 800 kg to 1,250 kg.
And it’s ISO 8611-compliant, guaranteeing the safety of both the load and the operators.
Pallet covers and smaller containers
When you need to secure stacks of containers on a pallet, the most versatile and cost-effective method to do so is to use pallet covers. The offer security during handling, even while removing the need to shrink-wrap the whole thing in plastic. Pallet covers additionally protect the load against dust and humidity.
Besides pallet covers, Schoeller Allibert offers a wide range of smaller containers that are perfect for automotive logistics, including:
Designed for automated handling, the VDA KLT series has a number of advantages, including high dimensional stability and robustness. The series allows for composite stacking, and its smooth inner surfaces are easy to clean. Its single walls mean low tare weight, hence more effective volume. The German Association of the Automotive Industry (VDA) is the leading association of German car manufacturers and suppliers. Standardization in the VDA is a central cross-cutting issue that affects all areas of the automotive industry.
Designed to be lightweight, have maximum internal space and achieve mechanical performance, this is the ideal stackable container range for automotive logistics. The Galia® robot grips were designed with the help of systems integration specialists. Featuring a standard European footprint, Galia® boxes are available in a range of sizes, have an RFID option and are interstackable with VDA, Eureka and other ranges. The Galia® standards are used among players in the French automotive industry (manufacturers, equipment suppliers, service providers and solution providers, etc.) The standard contributes to efficiency and performance.
Tech for automotive logistics
Schoeller Allibert offers various technologies that have specific benefit for the logistics chain of the automotive industry.
ESD. Multiple ranges of logistics assets, including RackPal®, EuroClick® and the KLT series, can be produced in ESD-approved conductive material. This protects electronic parts against electrostatic charges, and sets the standard for safe, reliable and secure transport of electronic components for the current and future automotive industry (including e-mobility).
SmartLink®. It’s a revolutionary idea whose time has come – and Schoeller Allibert is pioneering it: connect your logistical assets to the internet to make them track- and traceable. This makes asset management more convenient and efficient than ever, also preventing theft and loss, and lowering insurance premiums.
RFID. Fit your assets with RFID technology for a range of benefits, including fast, standardised and paperless data collection, simplified inventory management and smooth integration with ERP.
Anti-Slip. Schoeller Allibert’s anti-slip pallets stop cargo from sliding during handling and transport, offering extra protection to the packaged parts and reducing the risk of unwanted load shifting.
Want to know more about any of these products and services? Contact us at info@schoellerallibert.com
Contact us
Get in touchContact us
Inspiration
Related
Est proident veniam laborum exercitation est veniam reprehenderit nostrud officia. Ad Lorem aliquip duis labore duis. Irure deserunt eu minim culpa eiusmod quis ut sint eu pariatur magna aliquip et incidid voluptate cillum Lorem amet ea.
SASI® 4.0, an exciting year’s end gift for the logistics industry.
Year’s end is shopping season, with Black Friday, Cyber Monday (this year on 25 and 28 November) and of course Christmas as annual highlights. Consumers want what’s new and exciting, and it’s the job of the logistics ind...
Read newsThe Hoegaarden 24x0.25 L bottle crate
At Brau Beviale fair, end of November in Berlin, Schoeller Allibert displayed very innovative beverage packaging solutions: the Hoegaarden 24X0,25L bottle crate, unique as it can take bottle but also cardboard bottle pac...
Read news