Client Application: COOPERL Arc Atlantique
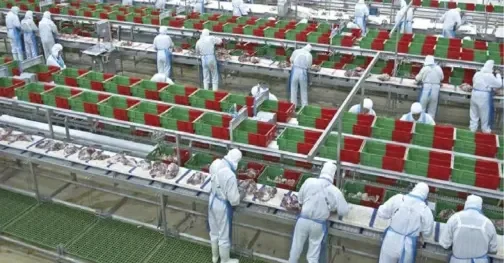
Industry
Contact us
Get in touchCooperl is one of the top pork meat processing companies in Europe. With 15 slaughtering and processing sites, Cooperl employs 4,800 people and revenue is more than 2 Billion Euros.
In 2005, Cooperl decided to invest massively in upgrading all processes and introduce automation to its major sites. Cooperl had different box models, not fully inter stackable, that could not be used with automated robotized systems because of base weakness.
Schoeller Allibert offered to customize a bicolor stack nest 600 x 400mm box , creating a specific variant to meet very challenging supply chain requirements , from deboning to consumer units packaging workshops, including blast freezing ,automated handling and storage in a robotized warehouse (shelf type).
Schoeller Allibert team worked closely with both the Cooperl development team, including IT, and the chosen system integrator to fine tune performances of both boxes and tracking devices. Among the severe requirements were 20kgs unit loads to be stored, with almost no base deflection, on shelves with supports 350mm apart.
Blast frozen cuts of meat unloaded by robots was also a major issue in terms of mechanical performance and resistance to repeated shocks at -30°C.
The Schoeller Allibert project team offered full tracking with ISO 15693 compliant read / write RFID tags. After 6 months real life trial, tags and boxes had proved outstanding resistance and reliability and the project went live.
Since, more than 250 000 boxes have been purchased by Cooperl, and daily more than 50 000 read / write operations are performed. All box moves, including deboning, secondary cutting and further processing, are piloted by the RFID writing-in and reading data.
Reliability has proved to be unsurpassed with less than 1/ 1000 misreading reported and the process speed could be increased each year according to larger volumes on each Cooperl Site.
Industry
Contact us
Get in touchContact us
Inspiration
Related
Est proident veniam laborum exercitation est veniam reprehenderit nostrud officia. Ad Lorem aliquip duis labore duis. Irure deserunt eu minim culpa eiusmod quis ut sint eu pariatur magna aliquip et incidid voluptate cillum Lorem amet ea.
Navigating EU Sustainability Regulations in Transport Packaging—A Roadmap for Compliance and Opportunity
We’re thrilled to introduce our latest whitepaper: New EU sustainability regulations and their impact on packaging. Designed as your essential resource, this whitepaper breaks down the complex, changing landscape of EU s...
Read newsDovecote park beefs up production with Schoeller Allibert containers
Containers from Schoeller Allibert have been selected by Dovecote Park, supplier of finest quality British beef, for use in its new cold store in Stapleton, North Yorkshire.
Read moreMaxiMeat® in meat retail logistics
Developed in partnership with a leading meat processing company and its major retail customer a few years ago, Maximeat logistics 800X600 Stack nest tray, is now the preferred solution for French retailers and is offered...
Read more