Magna Steyr Magnum Optimum application
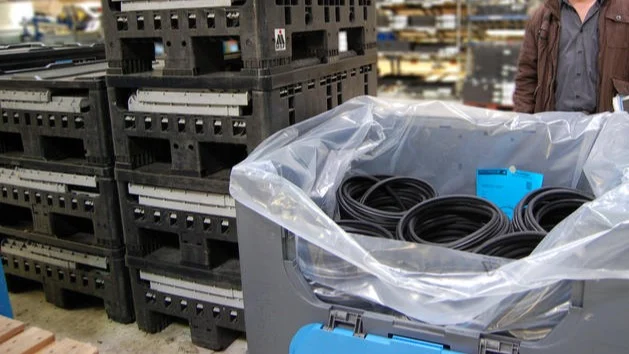
Industry
Contact us
Get in touchMagna Steyr Fahrzeugtechnik (MSF) based in Graz, Styria, and container producer Schoeller Allibert have a long-standing business relationship. For instance, when in 2002 BMW ordered its X3 to be assembled in Graz, MSF looked for a manufacturer of storage and transport containers and found in Schoeller Allibert a reliable and globally operating partner with a wide range of products. In 2003, a framework contract was signed. The plastic containers defined in this contract have ever since been among the automotive supplier’s standard containers, also beyond the location in Graz. These include, apart from the small VDA containers typical for the (German) automotive industry, the foldable large container MAGNUM with the standard dimensions of 1200 x 800 and 1200 x 1000 mm.
Over the years, large quantities of this model have been used. Currently over 10,000 pieces are in use at MSF.
Based on the experience from the cooperation with MSF and other major customers, Schoeller Allibert started analysing and researching how this already outstanding product could be even further improved and optimised. These efforts finally culminated in the Magnum Optimum.
“Thanks to new technical possibilities and our wealth of experience gained from practical use, we could improve several features. The new Magnum Optimum is, so to speak, an upgraded version of our already very successful container series”, says Martin Gansterer, authorised representative of the Austrian Schoeller Allibert location.
For one thing, wall thickness was reduced to provide larger internal dimensions, i.e. more space. When folded, it is flatter than any of the conventional large containers. For return transport, one jumbo truck can therefore accommodate 300 instead of the previous 210 folded containers. Moreover, the side walls as well as the doors of the Magnum Optimum are welded and have a smooth surface without ribs, which makes cleaning of the container easier and more economical.
Birth assistance for a new generation
MSF showed interest in the improved Magnum version early on and so several tests were run on 200 of the new containers together with selected suppliers. The tests delivered valuable insights for the developers at Schoeller Allibert, who could then add the final optimising touch to the container. “Thanks to our cooperation with Magna, all ‘growing pains’ could be detected and cured at an early stage so that the Magnum Optimum is today a very healthy product of Schoeller Allibert”, says Martin Gansterer, looking back on the cooperation with his customer, which played a significant role in the creation of the new container.
“Particularly in regular collective transport from and to suppliers, foldable containers come in useful. By choosing the Magnum Optimum, more empty containers fit into a truck, which really pays off over the year”, Oswald Friedl, responsible for logistics at MSF, explains the company’s great interest in the upgrade of the Magnum series. “Another asset is the smooth surface. Even when the empty containers are stored outside in the rain and are then unfolded, our employees or installation parts do not get wet”, Oswald Friedl adds.
After further tests and calculations, the Magnum Optimum was put on Magna’s list of standard containers and is now particularly put to use in the manufacturing of the Mini Countryman and Mini Paceman.
Standard container with options
Apart from the advantages described above, the new modular system of the Magnum Optimum offers a wide range of options for its users. Based on a platform concept, the modular system is built upon an ISO 1200 x 1000 mm pallet base, onto which exchangeable side walls of different heights can be fitted. Combined with the so-called Optiframe (base frame), the container walls can be raised to measure up to 1200 mm.
This option was the decisive factor for the Magna location in Ebergassing, Lower Austria, to acquire 60 Magnum Optimum containers in the summer of 2012. Intier Automotive Eybl (= Magna Exteriors & Interiors) had been looking for a transport container for the load floor of the Mercedes CLS Shooting Brake, which would be delivered from Sopron to Germany utilising load matching.
They wanted to avoid having to buy a special container and instead use an adequate standard container – which proved difficult considering the dimensions of the cargo. The traditional wire mesh container was too small and not suitable in terms of weight and ergonomics. The frequently used light-weight system made up of a pallet base, a foldable plastic ring and a lid was not stable enough for the required special height, and the necessary interior dunnage could not simply be returned in the folded containers. The Magnum Optimum extended by the base frame was the perfect solution that met all requirements: it is a stable, foldable standard container with extra height and ergonomically shaped folding doors that can also accommodate the interior dunnage when empty.
“At first, the Magnum Optimum wasn’t on our list because it was rather new. So now we are all the more satisfied with this solution. The container precisely matched the dimensions of the parts, allowing us to utilise the loading volume perfectly”, logistics planner David Guger says, pleased with the choice of the large container.
Thanks to its consistent base, the selected Magnum Optimum is, of course, compatible with all other versions of this container series. As a result, not only acquisition but also storage and transportation costs are considerably lower than those of special containers.
After a project has been completed, the base frame can be removed in a few easy steps and the standard-height container can be used for other purposes.
The Magnum Optimum not only combines decades of experience, its new concept also provides a multitude of options for the future. This makes the Magnum Optimum “flexible by default”.
Industry
Contact us
Get in touchContact us
Inspiration
Related
Est proident veniam laborum exercitation est veniam reprehenderit nostrud officia. Ad Lorem aliquip duis labore duis. Irure deserunt eu minim culpa eiusmod quis ut sint eu pariatur magna aliquip et incidid voluptate cillum Lorem amet ea.
Navigating EU Sustainability Regulations in Transport Packaging—A Roadmap for Compliance and Opportunity
We’re thrilled to introduce our latest whitepaper: New EU sustainability regulations and their impact on packaging. Designed as your essential resource, this whitepaper breaks down the complex, changing landscape of EU s...
Read newsGestamp Umformtechnik adopts the Magnum Optimum for inbound and internal logistics
Gestamp is one of the leading automotive suppliers worldwide. Specializing in steel parts and components, the Bielefeld plant needed to streamline the logistics of steel hollow frames supplied from Manchester in steel ca...
Read moreFoldable pallet containers at Continental
CONTINENTAL Automotive Czech Republic s r o, located in Turnov, is manufacturing and assembling pumps and engines modules for major OEM vehicles companies worldwide.
Read more